Quick Jump
Mis-shipments are a common occurrence in the world of order fulfillment, where even the most professional companies operate with around 99.9% order accuracy. However, this small percentage of error can significantly impact a company's bottom line, revealing the true costs hidden behind mis-shipments.
Mis-shipments can take various forms, including shipping incorrect items, sending the wrong quantity of products, delivering to an incorrect address, or failing to meet the delivery deadline. Each of these errors carries a cost, leading to the following financial implications:
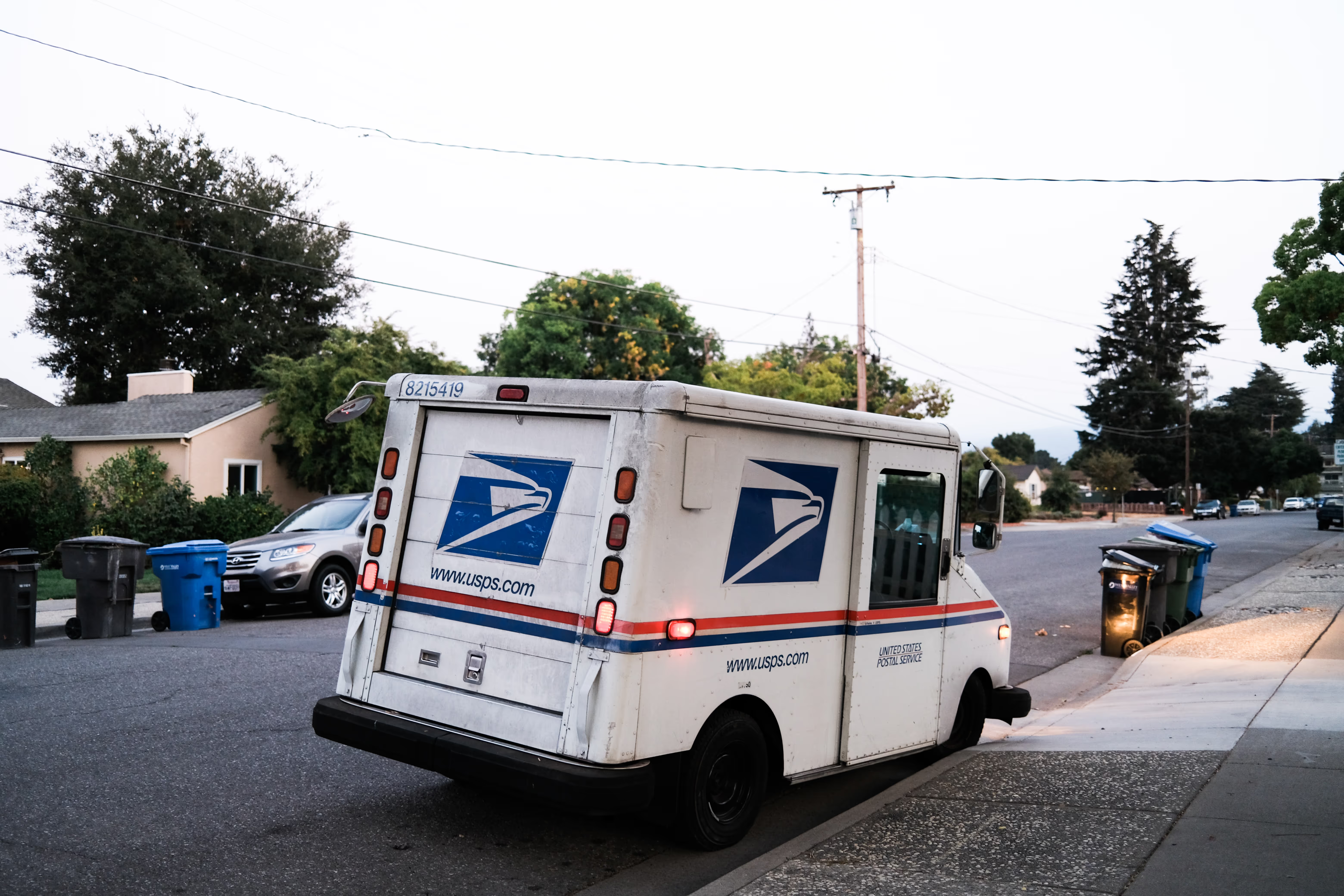
The Financial Implications of Mis-Shipment
1. Double Picking Time: Whenever a mis-shipment occurs, the time and money invested in picking and shipping the original order are lost. If a replacement order is necessary, you will incur the costs for picking and shipping again. This cost can range from $2 to $5 per pick and ship, taking 5 to 15 minutes each time. Considering the average wage of a warehouse worker, this cost can accumulate quickly.
2. Outbound Shipping Charges: When incorrect orders reach customers, they should not bear the cost of shipping. Therefore, outbound shipping charges fall on your business, which can range from $6 to $10 for small packages and up to $20 or more for larger, heavier ones.
3. Initial and Return Shipping Charges: If the customer decides to return the incorrect items, you'll have to cover both the initial and return shipping charges, adding to your costs.
4. Loss of Materials: The materials used to ship the original items often become unusable after a mis-shipment. This loss is minimal for recycled or standard packaging but can increase with custom packaging.
5. Return Processing Time: Returned items need to be checked for damage, costing an additional $2 to $3 per return. If the items are damaged, the loss extends to the cost of the items themselves.
6. Customer Service Expenses: Resolving a mis-shipment involves customer service time, which comes at a cost. For instance, a 15-minute call can cost as much as $21.45, based on average call center rates.
7. Additional Incentives: To maintain customer satisfaction, businesses often provide incentives Companies can suffer from massive financial losses due to incorrect deliveries.like waiving handling charges or offering discounts. This can add an extra $10 or more to your costs.
8. Customer Dissatisfaction: Mis-shipments can lead to customer dissatisfaction, resulting in lost future sales and potentially negative online reviews, damaging your brand's reputation.
Strategies to Minimize Mis-Shipment
Mis-shipments can cost businesses thousands of dollars each year. However, you can implement several strategies to improve order accuracy, enhance customer satisfaction, and preserve your bottom line.
1. Regular Inventory Checks: By conducting regular inventory checks, including quarterly checks, routine cycle counts, and annual audits, you can reduce errors and improve picking times. This is particularly important if you have inventory spread across multiple warehouse locations.
2. Utilization of Barcode Scanners and Warehouse Management Software: These tools ensure your team picks the right items in correct quantities. Some scanners can even update your inventory as soon as an item is picked, enhancing inventory accuracy.
3. Quality Control Checks: Implementing barcode technology and other quality control checks before sealing orders for shipping can help ensure order accuracy and prevent mis-shipments.
4. Efficient Returns Process: A well designed returns process can minimize the chaos of handling returns. It should aim to restock items as soon as possible and ensure the correct products are shipped to customers within a few business days.
Find the Best Warehousing and Fulfillment Company
To conclude, mis-shipments, while common, can carry significant hidden costs. By implementing effective inventory management strategies and quality control measures, businesses can minimize mis-shipments, saving time, money, and preserving customer satisfaction.
Remember, the goal isn't just to correct mis-shipments but to prevent them from happening in the first place. A focus on prevention will ensure timely and accurate shipments, leading to happier customers and a healthier bottom line.
Ready to eliminate the headaches of mis-shipments and simplify your fulfillment process? At Fulfill.com, we're experts in finding the perfect third-party logistics (3PL) provider tailored to your unique needs. Don't let mis-shipments derail your business. Start your journey towards seamless order fulfillment today!
Find your ideal 3PL partner here. Your future of hassle-free fulfillment is just a click away. Let us help you transform your logistics operations for the better.